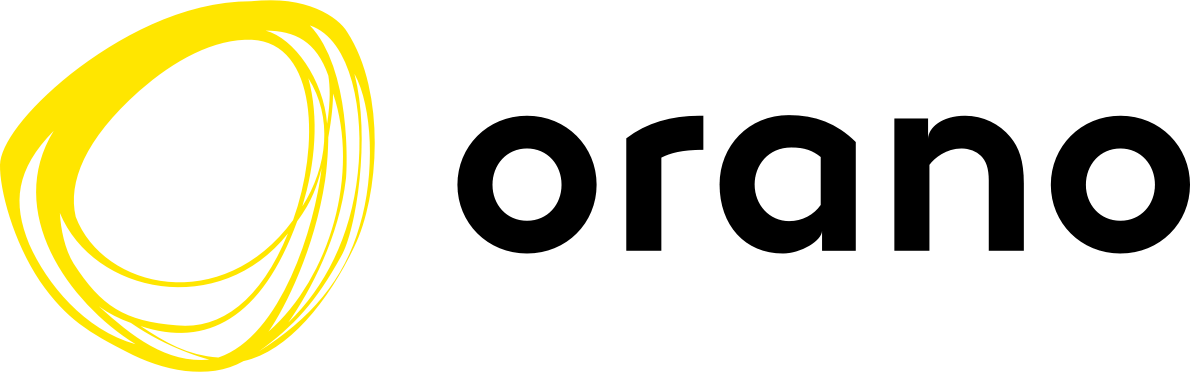
Orano is the first manufacturer in the world to have renewed its uranium conversion system. The Group operates in a price-aggressive sector, and integrating a host of technological innovations from large research & development programs has given it a competitive system with a reduced environmental footprint.
The Georges Besse II plant cost a total of 4 billion euros, and was inaugurated at the end of 2010. It has been operating at full capacity since the end of 2016. The new facility uses a completely different technology from the Eurodif production plant it replaces, and which is currently being dismantled.
Orano Tricastin chose the centrifuge process to optimize the enrichment of uranium with isotope 235. The technique is well tried and performs well. Find out more on our Expertise page.
With a yield of over 99%, the production of enriched uranium exclusively for civil use can supply the equivalent of 70 reactors across the world, and provide low-carbon electricity to around 90 million homes, equivalent to the combined population of France, Germany and the United Kingdom.
Controlled environmental impact
Enrichment by centrifuge uses fifty times less electricity than enrichment by gaseous diffusion (50 MW compared with 2500 MW), and does not require water from the Rhône for cooling. Also, the buildings have half the height of that of the current factory and do not cause noise pollution, so that the Georges Besse II plant is well integrated into its environment.
The intrinsic characteristics of the centrifuge process (it uses small quantities of materials and runs in vacuo) keep the overall risks to a minimum. The structures also meet the post-Fukushima standards regarding natural disasters.
Estimate for dismantling the Eurodif plant
Source : SFEN